Uteco has launched its Next 450 gravure press, designed to achieve faster job change, reduced setup time through automation, maximum-efficiency drying, and simplified controls in a centralised location.
Next 450 is the ideal solution for short and medium runs, fully automatic with innovative systems that reduce drastically waste of material, job changeover and energy consumption, said Uteco.
The inking system is enclosed to eliminate emissions and ink misting in the printing area, while the doctor blade is extremely rigid yet lightweight with a wide range of positioning controls (angle/point) at all cylinder sizes, said Uteco.
At the end of a job, the washed cylinders are expelled and new ones for the next job inserted through a semi-automatic trolley system, with a significant reduction in job change time. Next 450 is designed to work with both integral and hollow shaft cylinders.
Next 450 uses the Uteco ventilation system ‘CUBE’, which provides compact design, low noise, and optimum energy efficiency, said the company.
The drying capacity is achieved with hoods from 2.4m to 10m in length. They are characterised by air knives with brand new profile that improve the efficiency and uniformity of the air flow, and the laterally opening system allows total accessibility for cleaning/maintenance, according to the manufacturer.
Next 450 features single-location supervisory controls where all the machine settings can be accessed and maintained. A touchscreen supervisory HMI concentrates in one location all the process controls for quality management.
Next 450 can be customised with in-line technologies such as inline lamination, application of cold/hot glue, PVDC coating, digital print heads, laser die cutting units, and EB groups.

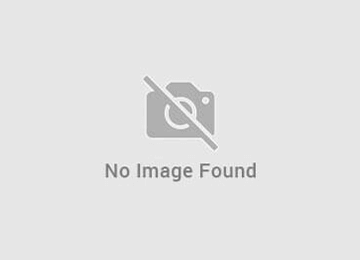
I would like to get updated news