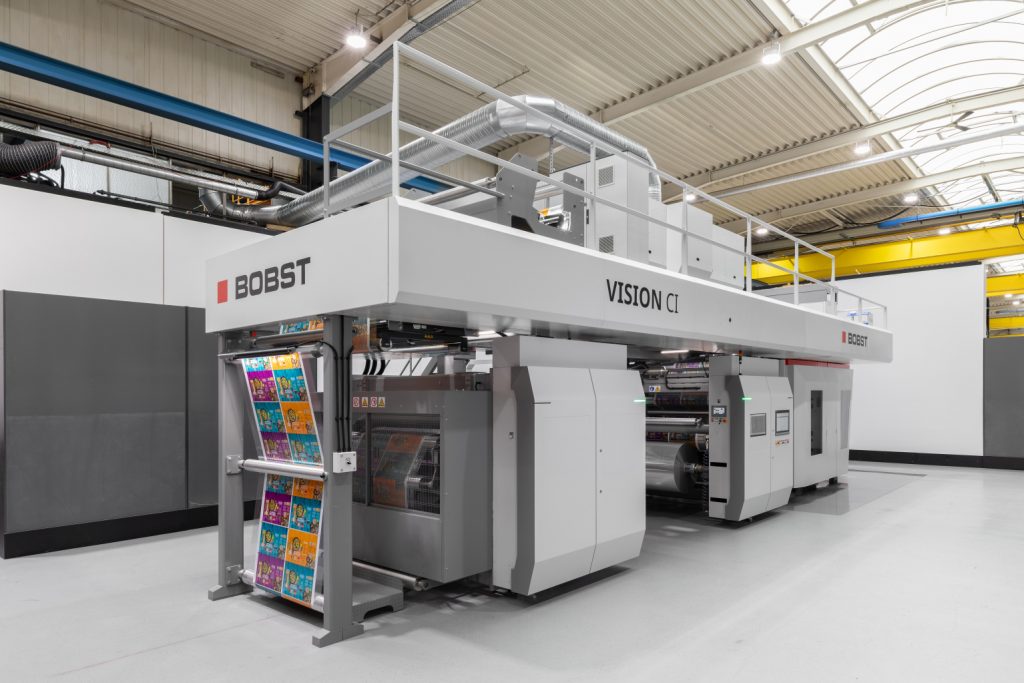
Bobst announced the launch of the BOBST VISION CI flexo press designed to deliver the most efficient performance for all production lengths on a wide range of substrates. Fast to set up and change over, it features technical innovations and automation that ensure repeatable process consistency, minimum waste and easy manufacturing.
The announcement comes during two major events for BOBST both taking place from 16 to 23 October – the K 2019 tradeshow in Düsseldorf, and an Open House event at Bobst’s Competence Center at Bobst Bielefeld, where attendees will be able to see the VISION CI flexo press in operation.
“With the VISION CI, Bobst has truly delivered on its vision for the future of CI flexo press printing,” said Mark McInulty, Managing Director CI Flexo Print-ing. “It combines the very latest technology with the highest manufacturing standards at the best price/performance ratio, putting premium print quality, reliability and highest standards of efficiency at the fingertips of converters everywhere.”
The VISION CI is available as an initially 8-color press and provides consistent and repeatable printing quality with solvent-based and water-based ink printing, on a wide range of substrate types and thicknesses. It has a compact and ergonomic, modular design, making installation and set-up very easy.
“From the moment the machine arrives, it can be installed and ready to print at the site in a matter of four weeks and this is a major benefit for converters,” said Mark McInulty.” Its compact dimensions will save valuable space, and its smart ergonomic design will ensure the operator a convenient, intuitive and fast operation. The VISION CI flexo press brings outstanding accuracy and repeatability of performance in terms of output quality and waste-saving operation to a wider number of flexible packaging printing operations.”
The VISION CI also brings substantial sustainability benefits. It contains ‘smartHEAT’ technology, which enables the machine to use its own heat as an internal and useful energy source, while its ‘smartCLEAN’ technology saves on ink and solvents. Furthermore ‘smartKEY’ and ‘smartSET’ will maximize machine productivity through minimizing job set-up time and material waste.