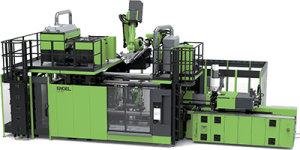
Austria: Engel has announced that it will be using the organomelt process to produce demo parts that reflect the latest innovations for car door modules at the K 2019 show in Dusseldorf, Germany.
The company claimed that in a world-first, its production cell will use infrared radiation to heat up and form three organic sheets of differing thicknesses, as well as shaping a high-quality visible surface in the same injection moulding process stage.
In yet another first, the company also claimed that the system will be equipped with three Engel easix articulated robots all operating at the same time.
“Thermoplastic composites are growing in importance when it comes to lightweighting in the automotive industry,” reported Dr Norbert Müller, head of Engel’s Center for Lightweight Composite Technologies.
There are two main reasons for this. Firstly, the consistent thermoplastic approach makes it possible to efficiently integrate the forming and functionalisation of fibre-reinforced prepregs, which reduces unit costs. Secondly, the use of exclusively thermoplastic polymers makes it easier to develop recycling strategies.
“Returning composite components to the material loop at the end of their service life is one of the priorities for ongoing development in the electric vehicle sector,” Müller noted. “Thermoplastic solutions are now becoming an increasingly frequent method, even within aircraft construction.”
Engel’s answer to the need for sustainable transport is organomelt. In the organomelt process, fibre-reinforced prepregs with a thermoplastic matrix such as organic sheets and tapes are heated, inserted into the mould, formed there and directly overmoulded with thermoplastic. The well-developed process has already been used in high-volume manufacturing, with Engel organomelt used for fully automated production of items such as front end carriers.
“In the future, several different prepregs will be combined for each component to tailor the lightweight construction characteristics to the relevant component’s shape as well as the different stresses on individual areas inside the component,” Müller explained. “The production cell at the K show will clearly demonstrate that great potential.”
The moulding process to be exhibited at K was developed in partnership with automotive supplier Brose.