The polymer specialist solution’s ability to compatibilise waste PE and PP will be a game-changer as it will reduce the need for costly and time-consuming materials separation when re-cycling plastics, Benjamim Daniel reports
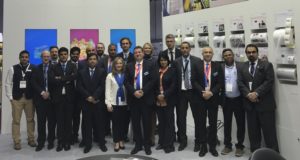
ExxonMobil knows what message it wants to convey to the MEA region with its Vistamaxx, a performance polymer while it is present at Arabplast 2019. It wants the visitors to understand what Vistamaxx can bring in terms of recycle value into the market and help customers to be more innovative and successful in their business. Of course, it also wants to expand its presence in the region.
“We are here to convey the ‘Rethink Recycle’ concept with Vistamaxx performance polymers. This solution allows low-cost recycling, targeting high-value applications,” says Gertrud Masure, market development manager, EMEAF for Vistamaxx at ExxonMobil, adding, “Vistamaxx is a specialty polymer; performance polymer that is used in many different applications. We are present as a film in stretchhood, cast stretch film / cast stretch wrap or as a toughening layer.”
Recycle operation
Vistamax goes in a lot of applications. If you add Vistamaxx in a recycle stream, you can improve the mechanical performance of that recycle stream and improve the process ability of that compound or re-granulate. Whether your stream is inherently more polyethylene based or polypropylene based that’s what we want to convey.
“We have done a number of tests and trials and we also have confirmations in the market from our customers,” Masure confirms.
Vistamaxx can be blended either to polypropylene or polyethylene. While Vistamaxx is the backbone in polypropylene, for polyethylene, it has a side function making it a good medium of compatibility between the polyethylene stream and polypropylene stream, which are usually not compatible.
Masure says, “With this, we can get the same clarity and stiffness as in PET. The challenge however is the processing side of all machinery that is something we need to work with them especially if they don’t want to invest.”
Switching challenge
ExxonMobil has been active promoting use of Vistamaxx among the plastic converters. Many brand owners, especially in the emerging world are hesitant if they don’t see any push from the government. However, the company still has some good names in the industry that are looking at sustainability and developing more sustainable solutions. “It is moving faster in countries like India because of legislation – the ban on multi component stretch. It’s moving very fast compared to countries like Egypt or here in the GCC where the push is not as big as in India. So it’s kind of a different pace.”
Then there’s Japan and US. “P&G is quite a good name in the US who use this. Unilever and Nestle are looking at developing new solutions. It is something that is coming not at a pace we would like to push but the industry has been designed, based on PET-PE laminate. It’s kind of most proven,” says Masure.
Will PET fade out? “No,” says Masure. “We have to understand that the world of PET is big enough and they don’t need it in printing.”
So to make packaging more sustainable, one can perhaps look at ‘mono-plastics’. It makes more sense because it’s easier to recycle such a structure and you don’t have to be clever to do that.
“PE is very stable for packaging. It adds a lot of value, gives more toughness, stiffness. You can also see it in printing. It is difficult for non-professionals to recognise if it is PE or PET. The print is clear and as accurate as PET. We took a big step by proving that it is possible now. All what we need is some help from the legislation. It’s helping us in India and I’m sure it will in this region as well,” concludes Masure.