R.K. Jain, Group President (Corp. F & A), Uflex Limited in an exclusive interview with Packaging Middle East and Africa explains how company’s extensive range of flexible packaging business activities beholds a future full of promising opportunities.
By April 2017, the aseptic packaging plant at Sanand in India’s Gujarat, will be commercially operational, confirming the dynamism and ambition of Uflex that eyes for a broad slice of the flexible packaging market. This plant for packaging liquid products is being set up with an initial investment of about USD 85 million.
With a targeted annual production of about 7 billion packs for packing products such as dairy products, energy drinks and other nonaerated liquids, the factory is part of what Uflex describes as a drive to complete its product bouquet that currently spans through packaging solutions for solids, semi-solids, powders, granular material, viscous fluids, gels, pastes. The only category that remains unattended today is packaging solutions for liquids. With 72 acres of land already at hand in Sanand, the flexible packaging behemoth may also consider expansion of the manufacturing facilities of its existing businesses.
Uflex’s capacity for manufacturing value added packaging products in India totals to about 100,000 TPA, while its packaging film manufacturing capacity in India, Egypt, Mexico, Poland, USA, and UAE, aggregates to around 337,000 TPA.
Group President (Corp. F & A), Uflex Mr.R.K. Jain told Packaging MEA in complete candour that Middle Eastern and African brands looking for a reliable partner for flexible packaging solutions can completely rely on Uflex for the product that is clearly a cut above the rest in terms of quality and the underlying technology. “While we can supply the packaging film from our manufacturing facilities at Jebel Ali (UAE) and Egypt, other value added packaging products can be sourced from our flourishing business in India.” said a confident Jain.
“If you talk about packaging in its basic form, it has now become extremely commoditised with several companies trying their hands in it,” he said. “I think what makes the difference is innovation to create sustained value added differentiation. At Uflex we customise the product to exactly map the requirements of our clientele world over. Coming to think of it, no two solutions that we offer will be the same. This capability puts us in a different league altogether. Not only do our packaging films but also our packaging products and other offerings like packaging machines, brand protection and anti-counterfeiting solutions (keeping spurious and look-alikes at bay), rotogravure printing cylinders; flexo-polymer plates; elastomers & sleeves, inks, adhesives, coatings and polyols etc. bring immense value for our customers.”, further added Jain.
“Our speed to market reach and the ability to process any quantum of order ensuring just in time (JIT) deliveries anywhere in the world makes us a preferred packaging solution partner. We have our indigenous team of engineers to commission the plants in the lowest possible time. Every little step adds up to the capacity and capability of Uflex as a Group. With best brains and the most contemporary technology by our side we have actually taken the flexible packaging industry as a whole to the next level” asserted Jain.
The company notably has 14 packaging film lines operating globally, and running in the most optimised manner.
Responding to a question about what differentiates Uflex from other players, Jain said, “Not everybody is able to run the plant at a speed of 500 metres per second. It’s like the speedometer in a car. Some people are comfortable driving only at 70/ 80 km per hour while others are even under control at the speed of 120. Something similar happens with plants too. The degree of productivity significantly varies from one company to the other. A big differentiating point is how one operates the plants? “At what efficiency level does one operate? How is one making the best use of available resources? We are able to run our plants at the designed capacities and with our soft skills, at times we have been able to derive much more than what the plant is actually designed for. This is a big plus. Where Uflex unquestionably differs from its peers is the fact that its business model covers the entire spectrum of flexible packaging solutions with an unwavering focus on meeting the customers’ requirements at all times. The fact of the matter is that we are fully integrated global flexible packaging solution provider. We make packaging films and also the value added packaging products like flexible packaging laminates (in roll form); prefabricated pouches, flexi-tubes (laminated) and big bags. We also manufacture the raw material for the polyester films i.e. the PET chips at our plant in Malanpur (India). As explained earlier we are further into packaging machines, chemicals, cylinders and flexo-plates/sleeves and entire gamut of brand protection/ anticounterfeiting or holographic solutions. This puts us in a great competitive stead to understand the ins and outs of the flexible packaging business and succeed.” emphasized R.K. Jain.
“When we work on new packaging products we simultaneously work on engineering the associated packaging machine so that we could offer our customers a holistic solution rather than a piecemeal portion. Uflex is a one stop solution meeting all flexible packaging needs.” exclaimed Jain.
“Over the years we have emphatically built upon these capabilities. This is what a solution-oriented approach for the business is all about.” He said. Elaborating more about the manufacturing model, Jain said. “The merit of our operation lies in its expanse. Starting from the PET chips (raw material) as one moves up the chain one can actually assess the value that goes into the making of a product till its fag end where the package is ready in all respects. Another point worth noting is that not only do all our businesses produce for in-house consumption, they also supply to the open market in their Individual capacities. Thus we are always abreast with the latest trends and technology at all junctures of the value chain”, he added.
“As a producer of packaging films, one of Uflex’s key considerations is sustainability” emphasized Jain. “We extensively research for reduction at source and associated light weighting. This significantly reduces our carbon footprint. Besides being low at source, our films and packaging products are re-cyclable and re-processable. Socioenvironmental sustainability is deeply embedded in our business model. Our first award on the international level for promoting eco-friendly products and responsible handling of packaging waste dates back to as early as 1994.” he told Packaging MEA.
For Jain, Uflex’s winning approach towards business stems fraom its roots, being established as Flex Industries back in 1985 by Mr. Ashok Chaturvedi, a ‘First Generation Entrepreneur’ who is fondly revered as the Father of the Indian Flexible Packaging Industry. Mr. Chaturvedi brought about a revolution in the Indian FMCG sector by introducing unit packs/ sachets for mouth fresheners, shampoos, ketchup etc in the eighties. With humble beginnings, Uflex under the aegis of Mr. Ashok Chaturvedi owing to his passion, commitment, grit, dynamism and foresight has now emerged as India’s largest flexible packaging solution company and a leading global player with consolidated revenue of USD 1 billion. “The pace at which we are innovating and growing, Uflex endeavours to double its revenue to USD 2 billion in 4-5 years.” said Jain summing up the conversation.

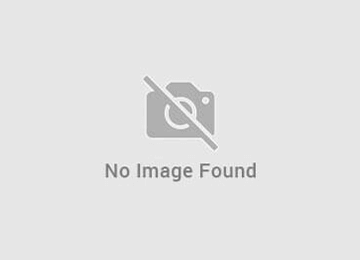