Growing demand for in-mould labelling (IML) looks set to open markets for the Germany-based converting specialist.
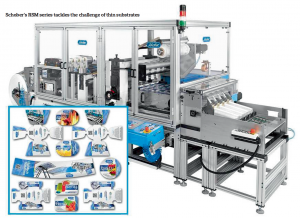
At Labelexpo Europe this September, visitors who paused at Schober’s stand got a preview of what could become a familiar sight in Middle East and African converting facilities.
In a setup with a V-stack spider stacker, the firm’s RSM rotary die-cutting machine demonstrated how thin substrates can be converted accurately and fast for a key regional growth area: in-mould labelling (IML).
For Schober, in fact, IML has already opened a significant market in countries such as the UAE and Saudi Arabia, said Hratch Borghosizian, managing director of Alpha, a local distributor.
“In this sector, Schober has a monopoly within the Middle East,” he said.
But shifts within packaging look poised to widen the region’s appetite for IML as global brands bring new products to emerging markets.
“I believe the printers are aware that IML is the future,” said Borghosizian.
“Before – five years ago – Schober’s IML machines installed in the UAE would rest. They are now fully used all the time.”
A pioneer in IML
In fact, Schober is now reaping the benefits of pioneering role in in-mould labelling over the last two decades, according to Denis Stephan, general manager and director of sales and marketing.
“We supplied the first machine in 1991,” he told Packaging MEA.
“But until the early 2000s, there was no business in IML. In the past, the suppliers were also mainly in Europe in the sheetfed business. But now people, wherever they are in the world, are looking for proximity suppliers.”
IML not only offers an ideal technology for the ‘no-label’ look, increasingly favoured for health and beauty products such as shampoos and some drink labels. This alternative to self-adhesive labelling can also cut out post-labelling operations – and the energy and labour costs they bring.
In the IML process, a label is placed in an empty mould into which plastic resin is blown, injected or inserted. The resin fuses with the back of the label to become an integral part of the object.
Three alternative technologies are used across different IML applications. While blow moulding is used for bottles and jugs, injection moulding and thermoforming dominate for open topped containers such as tubs or pails.
“So there are three families of products that are growing at double-digit rates,” said Stephan.
The thin substrates used in each approach pose special challenges in die-cutting, such as dealing with the static electricity generated by polyolefin films.
Schober’s RSM series caters for roll-fed materials from 260mm to 850mm in width, while the company’s Sheetline system tackles sheet-fed materials. To control and stack the very light pieces of material, the firm offers both M-Stack and S-Stack delivery systems.
The machine set up at Labelexpo demonstrated the Spider delivery system, a robotic device that enables several jobs to be ganged up on a single run, said Stephan.
“Right now, we are able to convert film and paper that is printed either by letterpress, gravure or digital printers, and the way of stacking that we have now – which is a robot stacking – can handle a variety of products in different shapes at high speed.”
IML’s growth in the MEA
For Stephan, the market for IML equipment in the Middle East is now set to grow in line with brands’ need for faster delivery.
“You cannot promote a new product in the dairy business if you have to wait for six weeks,” he said.
“That is also one of the reasons why, for us, the IML business is growing very fast. That machine is supplied worldwide, and right now there are more than 40 installations, including equipment in North Africa and the Middle East.”
He currently sees big demand in Saudi Arabia, driven by the IML’s use for its dairy products.
“It’s a trending market,” he said. “Obviously, the market follows the big manufacturers such as Nestlé or Unliver. If their marketing goes into a new country, their products go there and they try to manufacture containers.”
And IML offers several advantages for the big brands, including its ability to deter counterfeiting, as labels cannot be removed. In addition, IML enhances the durability of products and their decoration.
For Borhosizian, the benefits over longer established technologies are indisputable.
“Generally, the logic says brand owners always look for something sustainable,” he said.
“You get better print quality, it’s cheaper and it cuts a step in production.”
In his view, IML could eventually replace self-adhesive labels in most of its current applications, with machinery sales set for rapid expansion.
“In the UAE, over the next two years we should be looking for another two or three machines,” he said.